Winter is Coming again this year.
Duh...
Every year we get at least
one call in October wanting to know how quick we can build a ground
system. My standard answer is, "It will take about a week start
to finish for a single tower and probably less than 2 weeks for
multi-tower arrays".
The caller meant but didn't
state; "It is 33 degrees here today. Even though I have had my CP
for two and a half years, I have waited until the forecast is calling
for a FREEZE warning and I still haven't gotten my station built.
AND the CP runs out in January. How QUICKLY can
you drop everything and get my station built before winter?"
Winter work in general costs
more than fair weather work. Equipment preparations, clothing
requirements, speed of work, length of work day, weather delays ALL
cause winter weather work to be more expensive than summer work.
Not to mention the impact on safety. Restricted vision, dexterity
and movement are serious concerns when working on and around heavy
equipment.
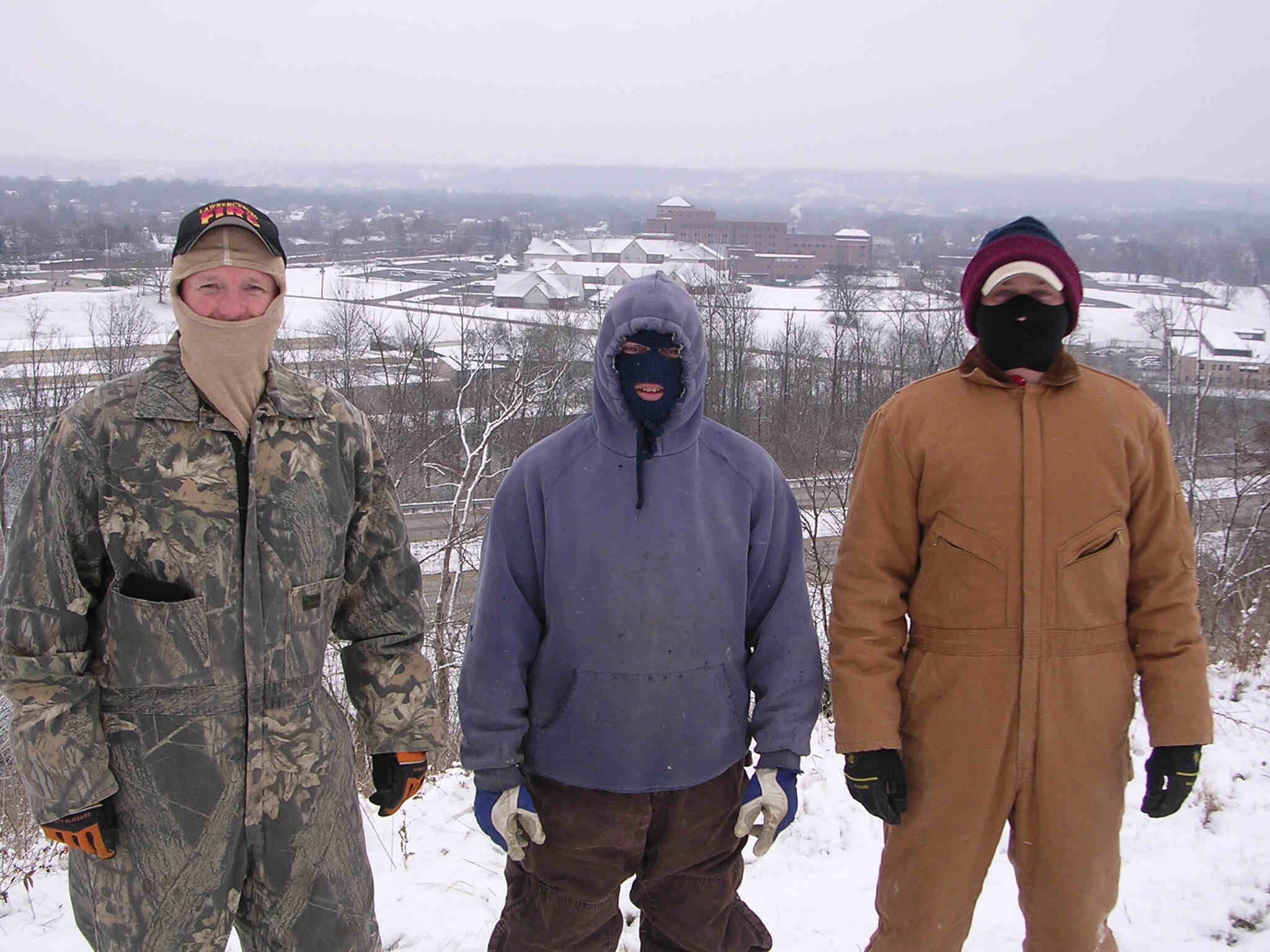
As anyone involved in
building broadcast stations is aware, more government agencies have
their fingers stuck in the radio business more than maybe even the
Nuclear Power industry (I could be mistaken on this). Three years
can barely be enough time by the time all of the acronym's are
satisfied.
HOWEVER, most of the
rush-before-winter projects that we do are for one of 2 reasons:
-
Procrastination
I'll get that done
tomorrow! Or the next day! Maybe... If I get to it... Oh...
Hey! Its October... Again.
More time and money is
wasted on site construction because of procrastination than any other
preventable cause. RUSH costs money. Getting materials in a
hurry costs more, travel costs more, guaranteeing delivery of other
materials and services cost more, etc, etc.
-
Saving Money
I have provided
proposals to stations that have point-blank told me that I was too
expensive. They hunted around and found someone that said that
they could do the work for a small percentage of my proposal (see my treatment of the exceeding cheap quote).
And then they never show up. On one memorable project, it cost
the client almost 50% more than my original proposal from a year
earlier. Materials and mobilization were up due to availability
and market factors. Shipping was astronomical due to speed,
weight and location factors. Mobilization was driven up by lack
of advance purchase time. Rush costs money. Extra labor was
required to finish by the CP expiration.
I have also had a RUSH
client tell me that they would have called AGSC to start with but had
been convinced by someone that they could do the job cheaper than
anyone around. They were absolutely correct. The work was
never done, henceforth, it cost the station NOTHING! Until
we/they had to pay expedited shipping charges and shuffle properly
planned projects around. RUSH costs money.
Regulatory delays comprise a
fairly small portion of our compressed time line work.
When we (Or anyone. Even
you.) order materials and make travel plans on a compressed time line,
the costs will be higher. Every facet of the project
will usually be impacted when adhering to a compressed time line.
The more compressed, the more expensive. Rush costs money.

We Specialize in Compressed Time Line Projects
We have the resources,
equipment and knowledge to make a project "happen" just in time.
By saying that we specialize in compressed projects doesn't mean that
we encourage or like them. Just that we can "git 'er done" if
needed.
Some tips to help make your
project go a little smoother.
-
Choose your venders and
contractors (tower, ground system, building, utilities, equipment, etc)
early. You should already be talking to venders and contractors before
the initial application is filed. Contractors and equipment
should be lined up AS SOON as the CP arrives. Even if the
proposed construction date is months away.
-
Choose your venders and
contractors wisely. A great deal isn't necessarily a good value.
-
Avoid the
"Delay Snowball". Don't schedule unrealistic time frames for
work. Allow plenty of time for all phases of your
project. Defining an overly strict time line often results in
unexpected delays. It is often the case where a single short delay at the
beginning of a project becomes a significant delay at the end of the
project. This typically happens when the project planner
schedules project events too tightly. If one contractor has a
delay (materials, weather, etc) it is often the case with tightly
scheduled projects that the next contractor in line cannot wait out the
delay and has to go to another project. Then the third contractor
can't comply with the new time frame and is another week or two getting
to the site, and the 4th contractor had to proceed with another project
and will be weeks more getting there, etc, etc, etc. A few days
delay at the beginning of the project results in the project being
weeks over scheduled time due to the schedule being too optimistic and
compressed. Delays are NEVER cumulative but grow at exponential
rates. IE, the "Delay Snowball".
-
Ask for references.
-
Regularly follow up on
equipment delivery, construction dates and contractor status.
-
Know EXACTLY what
permits and permissions will be required BEFORE you file your
application. Moving to another site may save a large sum of money
if permits or remediation can be avoided.
-
Contractors should be in
touch with each other for coordination. However, SOMEONE (you,
your engineer, GC, or even myself as a site coordinator) MUST
be in overall control of the time line AND scheduling.
-
Return contracts,
proposals and payments according to the vender/contractor
requirements. Failure to return a contract or payment in a timely
manner may result in unplanned delays.
-
Go to the doctor.
Get something for your stomach and something for your head. The
larger the project the more/better something you may need. For
the humor challenged, this is only half joking. Especially if you
didn't contract AM Ground Systems Company.
|